ابزار دقیق و کنترل فرآیند در کوره خلاء

ابزار دقیق و کنترل فرآیند در کوره خلاء
نوع و قابلیت اطمینان ابزار دقیق و کنترلهای فرآیند مورد استفاده در کوره خلاء در صنعت عملیات حرارتی (شکل 1) هم برای عملکرد خود کوره خلاء و هم برای نتایجی که هنگام پردازش اجزای حیاتی بهدست میآیند، حیاتی است.
دست کم نمیگیریم اگر بگوییم با توجه به طول عمر تجهیزات خلاء، ابزار دقیق و کنترلها باید هر چند سال یکبار بهروزرسانی شوند تا از پیشرفتهترین فناوری ممکن استفاده شود
(به عنوان مثال، ارتباطات و تشخیص از راه دور، نظارت و کنترل فرآیند توسط اینترنت مبتنی بر اینترنت). دستگاه ها و مانند آن).
تقاضا در بسته های ابزار دقیق و کنترل کوره خلاء
کنترل دما و در نتیجه یکنواختی دما به دلیل ویژگیهای انتقال حرارت کوره هنگام حرکت میتواند دشوار باشد، به عنوان مثال، از همرفت به گرمایش تابشی و انتقال حرارت همرفتی/رسانا در طول خاموش کردن.
بعنوان مثال، توانایی تغییر نرخ گرمایش کوره (به عنوان مثال، 3 درجه سانتیگراد در دقیقه – 25 درجه سانتیگراد در دقیقه) نیاز به اندازه گیری و کنترل دقیق و دقیق دارد، از جمله کنترل برنامه نقطه تنظیم با ویژگی های خیساندن تضمین شده.
کوره خلاء اغلب برای انواع محصولات و فرآیندها توسط عملیات حرارتی استفاده می شود و مدیریت دستور پخت را به یک عملکرد مهم تبدیل می کند.
بیش از حد دمای نقاط تنظیم معمولاً مجاز نیست. کنترل برنامه نقطه تنظیم اغلب برای دما، سطح خلاء و فشار گاز با تعامل گسترده بین این برنامه ها و همچنین با کنترل منطقی اعمال میشود.
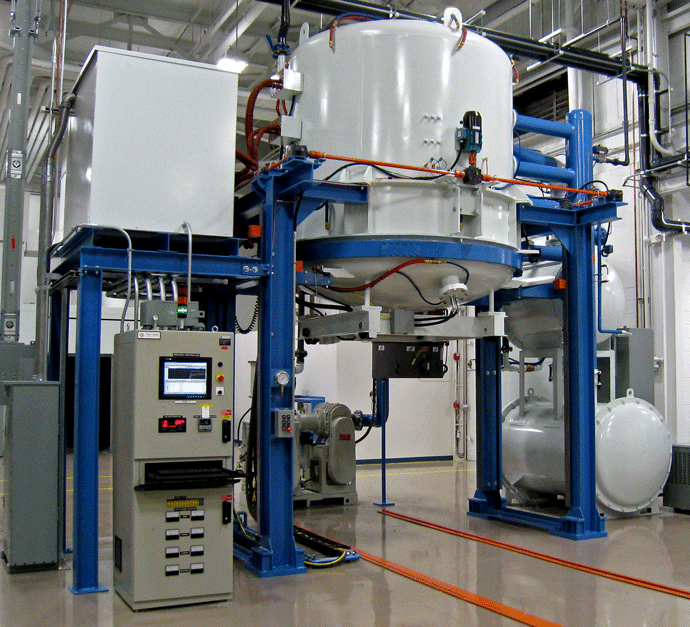
با توجه به تنوع کاربرد فوق العاده کوره خلاء (به عنوان مثال، بازپخت، لحیم کاری، سخت شدن مورد، پیوند انتشار، سخت شدن، ذوب، معتدل کردن، رسوب لایه نازک) و نیاز به پردازش این مواد در محدوده وسیعی از دما،
معمولاً بدون واکنش سطحی (مثال اکسیداسیون) انتخاب بسته ابزار دقیق تر، متنوع تر و پیچیده تر می شود.
چه با فشار جزئی برای جلوگیری از تبخیر عناصر مختلف موجود در مواد، چه در فشار بیش از حد برای بهبود یکنواختی دمای پایین، کنترل فرآیند (دما، خلاء) الزامی است.
مثال فرآیند
کوره های خلاء برای عملیات حرارتی و لحیم کاری معمولاً کوره های تک محفظه ای هستند که چرخه های دسته ای را انجام می دهند.
چرخه های دسته ای بین فرآیندها متفاوت است، اما معمولاً به تنظیم دما، خلاء و منطق توالی نیاز دارند. دما و خلاء به طور گسترده با منطق تعامل دارند.
یک چرخه عملیات حرارتی معمولی پس از بارگیری محصول در کوره و بسته شدن درب شروع می شود. برخی از کاربران کوره را ایمن می کنند و قبل از ادامه آزمایش نشتی را انجام می دهند.
یک پمپ خلاء زبر فشار را تا حدود 0.05 torr (50 میکرون) کاهش می دهد. یک پمپ انتشار اختیاری می تواند فشار را به زیر 1 x 10-3 torr (1 میکرون) کاهش دهد.
برخی از فرآیندها به گاز بی اثری مانند آرگون نیاز دارند که با سرعت جریان کم به کوره وارد شود و به فشار اجازه می دهد تا حدود 0.50 torr (500 میکرون) یا بیشتر افزایش یابد – این بخشی از دستگاه های کنترل فشار جزئی است.
با افزایش دما و تبخیر شدن آلاینده ها، فشار افزایش می یابد. کنترل خلاء در حدود 0.50 torr (500 میکرون) در فرآیندهای فشار جزئی یا کمتر از 10-4 حفظ می شود.torr در فرآیندهای خلاء بالا.
اگر خلاء بیش از یک مقدار خاص از نقطه تنظیم خاص منحرف شود، برنامه دما تا زمانی که شرایط اصلاح شود، نگه داشته می شود. برنامه دما از یک سری رمپ و خیساندن عبور می کند.
پس از خیساندن در دمای بالا، فرآیند کوئنچ فعال میشود و اجازه میدهد دما کاهش یابد. افزایش جریان گاز بی اثر (به عنوان مثال، نیتروژن، آرگون، هلیوم) و گردش آب خنک کننده در دیواره های کوره و مبدل حرارتی کار را خنک می کند.
خنک کننده فشار کوره را کاهش می دهد و به کنترل فشار اضافی نیاز دارد. در طول سرمایش، فشار معمولاً بین 0.85 بار تا 10 بار بسته به نوع فرآیند کنترل می شود.
یک چراغ یا بوق معمولاً به عنوان نشانه ای به اپراتور فعال می شود که چرخه کامل شده است.
اجرای کنترل
طی 40 تا 50 سال گذشته، تولیدکنندگان کوره های خلاء از پلتفرم های سخت افزاری مختلف برای کنترل تجهیزات و فرآیند استفاده کرده اند.
یک پلتفرم مشترک مبتنی بر کنترلر هیبریدی Honeywell HC900 همراه با نرم افزار Experion HS R500 SCADA است. از ویژگی های این پکیج می توان به موارد زیر اشاره کرد:
ویژگی های Honeywell HC900 Experion HS R500 Process Control
کنترلر هیبریدی HC900 همراه با رابط Experion HS R500 (شکل 2) برای استفاده کارآمد، ایمن و سازنده در تجهیزات خلاء با حداکثر راحتی اپراتور طراحی شده است. برخی از توانایی های آن عبارتند از:
- کنترل برنامه توالی و متغیرها در مقابل زمان
- کنترل حلقه تعدیل کننده متناسب (PID).
- توابع منطقی برای وضعیت تجهیزات و فرآیند
- تشخیص زنگ هشدار، اعلام، و ورود به سیستم
- جمع آوری داده ها و ثبت داده ها
- پیکربندی دستور غذا، ذخیره سازی محلی، و قابلیت دانلود
- به راحتی توسط اپراتورها در واحدهای مهندسی قابل برنامه ریزی است.
- شانزده (16) رویداد قابل برنامه ریزی برای ادغام با توابع کنترل توالی.
- هشدارها و رویدادها ممکن است برای ارسال یک پیام ایمیل برنامه ریزی شوند.
- پروتکل Modbus/TCP امکان اتصال به نرم افزار HMI، اکتساب داده و سرور OPC را فراهم می کند.
- پورت اترنت از اتصال مستقیم رایانه شخصی یا اتصال مودم خارجی برای آپلود، دانلود و نگهداری پیکربندی پشتیبانی می کند.
- ورودی های آنالوگ ایزوله و جهانی امکان ترکیبی از انواع ورودی آنالوگ را در همان کارت فراهم می کند و هزینه ورودی/خروجی را کاهش می دهد.
- تنظیم خودکار و حفاظت بیش از حد فازی برای راه اندازی سریع و عملکرد کنترل مناسب
- ذخیره سازی تا 1000 دستور غذا برای انتخاب سریع و بدون خطا محصول
- ذخیره سازی تا 1000 پروفایل زمان/دما. هر نمایه ممکن است بخشی از یک دستور غذا باشد.
- هر HC900 می تواند تا 8 کنترلر همتا را برای تبادل داده های آنالوگ یا دیجیتال از طریق اترنت پشتیبانی کند.
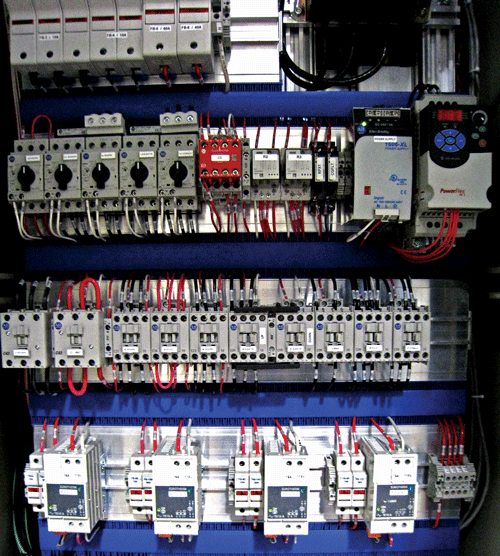
نمونه سیستم کنترل کوره خلاء
کنترل دما با یک مجموعه الگوریتم داخلی که قادر به رسیدگی به اکثر نیازهای برنامه است اجرا می شود. ثابت های تنظیم چندگانه ممکن است برای تطبیق پاسخ کنترل به ویژگی های دینامیکی کوره استفاده شود.
محدودیتهای رویکرد حداکثر نرخ گرمایش را بدون افزایش بیش از حد، کاهش زمان چرخه و بهینهسازی راندمان میدهد. HC900 توابع برنامه نویس نقطه تنظیم، حلقه و منطق را در یک دستگاه ادغام می کند.
قابلیت Setpoint Program HC900 برای کنترل پروفیل های دما با حداکثر 1000 پروفایل مختلف مناسب برای طیف وسیعی از محصولات استفاده می شود که می توان برای استفاده در هنگام پردازش این محصولات ایجاد و ذخیره کرد.
یک پروفیل چرخه عملیات حرارتی معمولی (شکل 3) از عملکرد خیساندن تضمینی بار (به عنوان رویداد 7) برای کنترل دمای بحرانی خیساندن استفاده می کند.
نمایه چرخه همچنین شامل رویدادهای دیگری است که برای کنترل عملکردهای مختلف مورد نیاز یک چرخه عملیات حرارتی (سطح خلاء بالا و پایین، فشار جزئی، خاموش کردن و غیره) استفاده می شود.
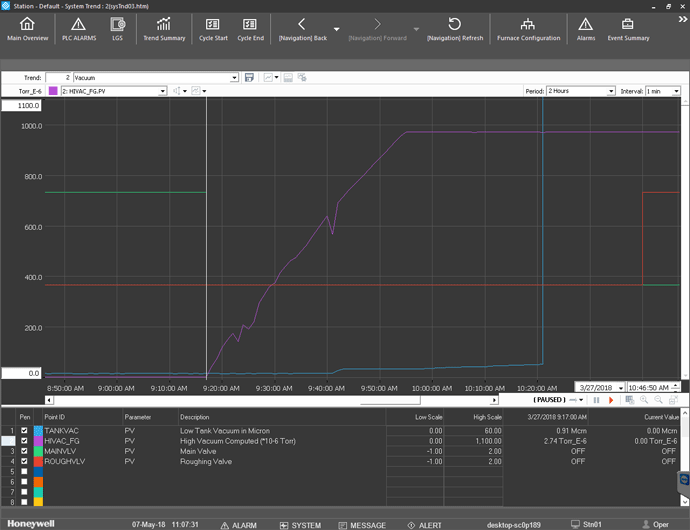
یک پایگاه داده قابل تنظیم، هم توابع حلقه (متناسب، تعدیل کننده) و هم توابع منطقی (گسسته، بولی) مورد نیاز فرآیند را یکپارچه می کند.
نمایشگرهای کاربر پسند اپراتور اطلاعات پویا در مورد وضعیت هر اجرا را در حین پیشرفت در اختیار اپراتور قرار می دهد. هشدارها به صورت رنگی در نمایشگرهای اختصاصی اعلام می شوند و می توانند مستقیماً از رابط اپراتور تأیید شوند.
قابلیت اکتساب و کنترل داده ها HC900 به تجزیه و تحلیل فرآیند مداوم برای تعریف و اجرای استراتژی های کنترلی مختلف اجازه می دهد.
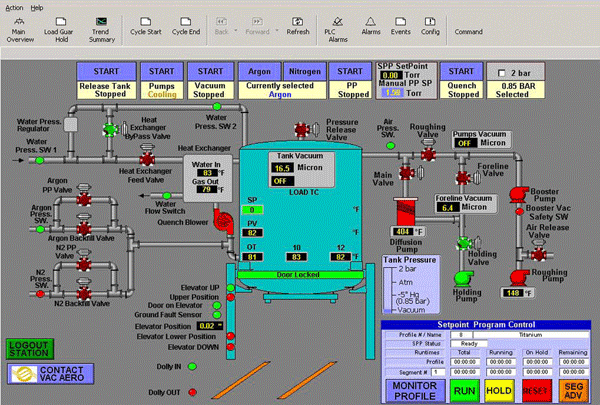
پیاده سازی
HC900 یک کنترلر نصب شده روی پنل است که به یک رابط اپراتور مبتنی بر کامپیوتر متصل است.
تمام سیگنال های میدانی به کنترلر ختم می شوند. این کنترلر دارای ورودی های آنالوگ جهانی، خروجی های آنالوگ و طیف گسترده ای از انواع ورودی و خروجی دیجیتال است.
این کنترل کننده تمام عملکردهای کنترل کوره خلاء را ارائه می دهد.
پیکربندی
ابزار Hybrid Control Designer (شکل 4) تکنیک های پیکربندی پیشرفته ای را ارائه می دهد که امکان پیاده سازی انواع استراتژی ها را به راحتی فراهم می کند.
قابلیت نظارت و ویرایش پیکربندی حالت اجرا به این امکان میدهد تا با کسب دانش فرآیند، این استراتژیها آزمایش و اصلاح شوند.
نظارت بر عملکرد کامل را می توان از روی صفحه نمایش کنترل و کنترل کرد. نمایشگرهای استاندارد و سفارشی، یادگیری و استفاده از سیستم را برای اپراتورها ساده می کند (شکل شماره 5 – 9).
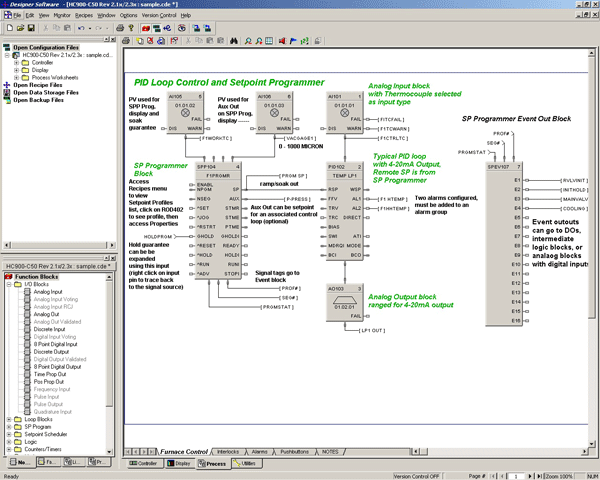
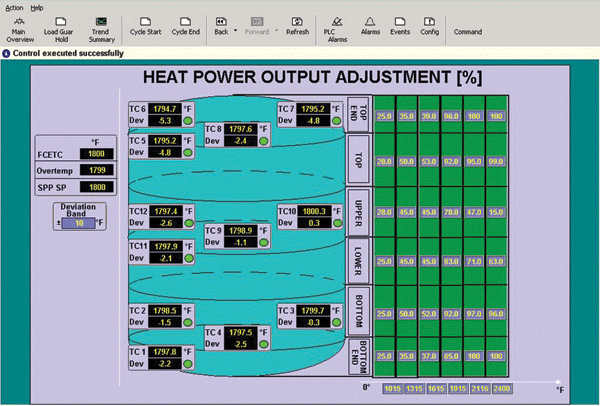
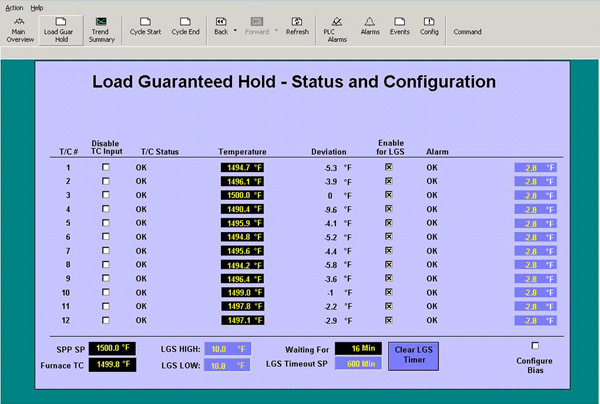
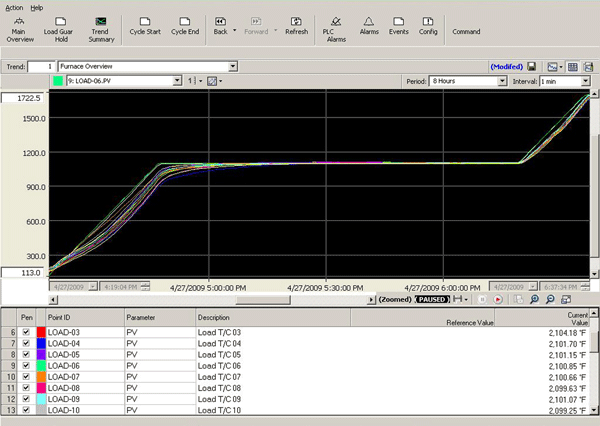
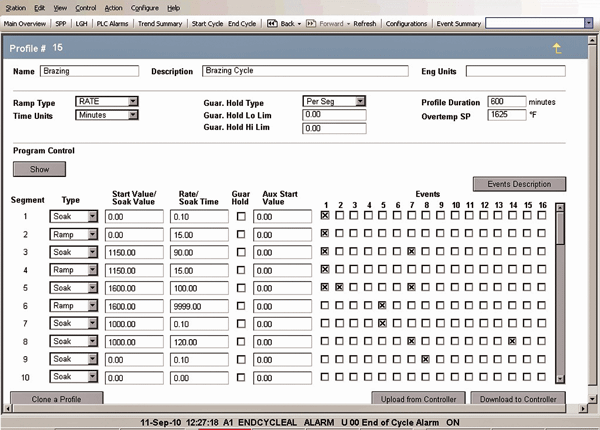
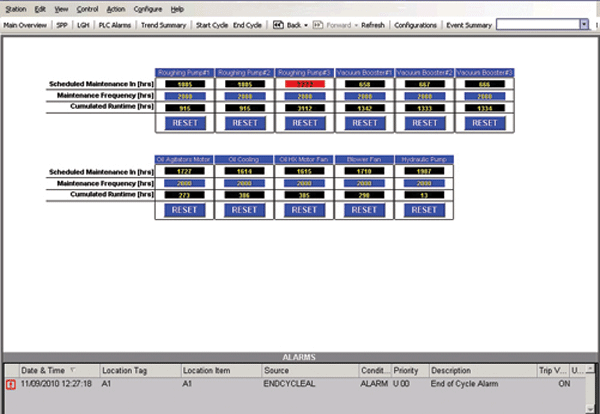
جمع آوری و ذخیره سازی داده ها
جمع آوری و ذخیره سازی داده ها در سیستم نظارت انجام می شود و شامل انواع عملکردهای گزارش دهی است. برخی از این موارد عبارتند از:
- هشدار / گزارش رویداد همه آلارم ها و رویدادها را در یک دوره زمانی مشخص گزارش می کند.
- گزارش مدت زمان هشدار زمان وقوع و زمان سپری شده قبل از بازگشت به حالت عادی را برای آلارم های خاص در یک دوره زمانی مشخص گزارش می کند.
- پیجر زنگ هشدار (اختیاری). هشدارهای نقطه تنظیم ممکن است به یک سیستم پیجینگ هشدار یا پیام رسانی ارسال شوند.
- گزارش یکپارچه اکسل امکان راه اندازی یک گزارش ساخته شده با استفاده از Microsoft Excel را فراهم می کند.
- گزارشهای دستهای، تاریخچهای را برای نقاط و رویدادهایی که در طول یک فرآیند تولید فرآیند رخ دادهاند، جمعآوری میکند. همچنین ممکن است داده های دسته ای استاتیک مانند شماره دسته، نام مشتری، اندازه لات و غیره به گزارش اضافه شود.
- برای وارد کردن اطلاعات دسته ای می توان از عملکرد داده های نوارکد شده استفاده کرد.
- گزارشها ممکن است به صورت دورهای یا بر اساس رویداد یا تقاضا ایجاد شوند. خروجی گزارش ممکن است برای تجزیه و تحلیل یا مشاهده الکترونیکی به صفحه نمایش، چاپگر، فایل یا مستقیماً به رایانه دیگری هدایت شود.
- مجموعه تاریخچه در طیف گسترده ای از فرکانس ها در هر دو فرمت متوسط و عکس فوری/تولید در دسترس است. با آرشیو خودکار امکان نگهداری و دسترسی به مقادیر نامحدودی از داده های تاریخی را می توان مقدار زیادی از تاریخچه را بصورت آنلاین حفظ کرد.
- پیکربندی روند انعطاف پذیر اجازه می دهد تا روندها را پیکربندی کنید. داده های زمان واقعی و تاریخی با هم در یک روند ارائه می شوند.
- ویژگی ذخیره سازی داده ها را می توان برای ثبت اطلاعات پردازش در طول چرخه به دیسک سخت داخلی یا یک دستگاه ذخیره سازی شبکه کارخانه برای ثبت دائمی استفاده کرد.
توابع زنگ هشدار کوره خلاء
این نرم افزار بگونه ای بهینه شده است که تمامی شرایط عملیاتی و زنگ هشدار را پیش بینی کند.
این نرم افزار همچنین کنترل نظارت و جمع آوری داده ها (SCADA) را با استفاده از صفحه نمایش لمسی LCD برای رابط اپراتور برای ویژگی هایی مانند:
- سازگاری با SCADA در سراسر کارخانه و یکپارچه سازی شبکه.
- اعتبار سنجی چرخه فرآیند
- هشدار و مدیریت رویداد و گزارش گسترده.
- کنترل دما با استفاده از الگوریتم های پیشرفته، تنظیم خودکار، و برش دیجیتالی چند ناحیه ای.
- امنیت ورود/خروج اپراتور برای محدود کردن کنترل اپراتور بر عملکردهای فردی.
- مدیریت نگهداری و عیب یابی پیشرفته.
- مجموعه گسترده ای از الگوریتم های پیشرفته برای حداکثر عملکرد فرآیند
- اتصال اترنت را از طریق پروتکل Modbus/TCP باز کنید که دسترسی به فرآیند و جمع آوری داده ها را در سطح کارخانه فراهم کند.
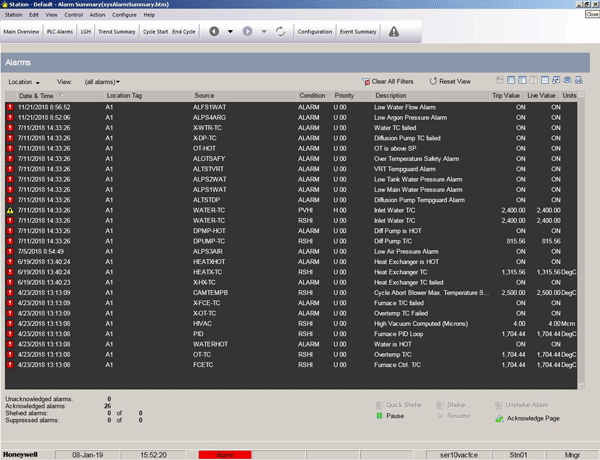